3D Printing and Its Impact on the Design of Mixing Equipment Components
The advent of 3D printing—also known as additive manufacturing—has sparked a revolution in industrial design, enabling engineers to create complex, optimized mixing components previously deemed unmanufacturable. In mixing technology, this innovation is more than a novelty—it enhances performance, saves cost, and accelerates development cycles. In this article, we explore how 3D printing reshapes the design of mixing equipment parts like impellers, static mixers, and micro-reactor elements, and what this means for industries ranging from pharmaceuticals to 3D printing materials themselves.
What Makes 3D Printing a Game-Changer for Mixing Components
3D printing allows the fabrication of intricate geometries—lattices, channels, and internal cavities—that traditional manufacturing methods struggle to achieve. This design freedom supports lightweight structures, improved flow dynamics, and part consolidation. Designers can now rethink impellers and static mixer elements using Design for Additive Manufacturing (DfAM) principles. For instance, a single 3D-printed impeller could replace multiple bolted parts while offering superior fluid mixing performance due to its optimized shape.
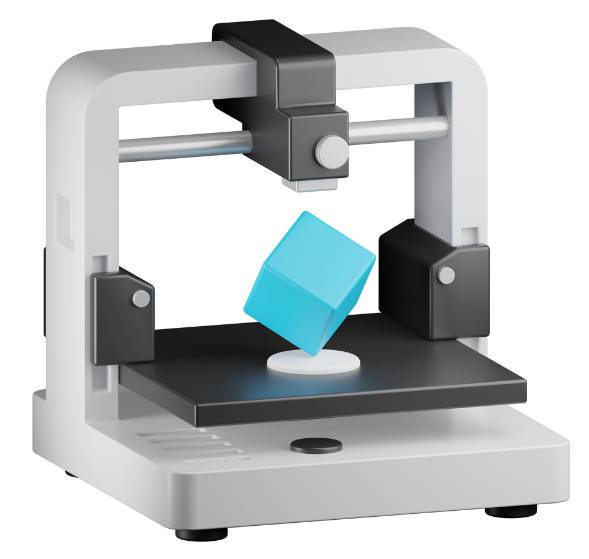
Custom Impeller Designs and Printing Materials
Enthusiasts frequently share custom 3D-printed mixer impellers—like those compatible with power drills—on platforms such as Reddit, highlighting the community’s fascination with rapid prototyping. While DIY models are proof of concept, industrial-grade impellers require materials like nylon, PETG, or even metal resins for durability. By optimizing printed materials for strength and surface finish, manufacturers can prototype new impeller designs cheaply and test flow efficiency before committing to costly machining or casting.
Microfluidic Mixing via 3D-Printed Static Mixers
Beyond large impellers, 3D printing excels at producing microfluidic static mixers, such as staggered herringbone mixers (SHMs) used in laminar-flow applications. Researchers at UC have demonstrated that 3D-printed SHM prototypes rival lab-fabricated molds in performance while offering faster, more affordable iterations. With applications spanning drug discovery to chemical analysis, these mixers highlight additive manufacturing’s advantage at micro scales.
Real-Time Testing in Lab-Scale Reactors
Scientific studies have shown that 3D-printed mixers can dramatically improve fluid blending in millimeter-scale reactors, especially when combined with real-time visualization methods like colorimetric pH films. Printing customized reactor channels with embedded sensors demonstrates how additive manufacturing enables experimenters to iterate design, test, and integrate detection methodologies within a single device—driving innovation and accelerating insights.
Industrial-Scale Mixing: Bridging with 3D Printing
Notably, major industrial players employ 3D-printed static mixer inserts for specialized applications. For example, static mixer geometries can be customized to reduce membrane fouling in tubular filtration systems. One study showed a 140% increase in filtrate flow using twisted-tape inserts produced through additive manufacturing arxiv.org. This showcases real-world gains in performance and energy efficiency when conventional components are redesigned with 3D printing in mind.
Specialized Mixers for Additive Manufacturing Materials
Some mixers manufactured by companies like Resodyn Acoustic Mixers play a dual role—mixing materials for 3D printing and being designed using insights gained from 3D printers themselves. These mixers optimize the preparation of powders, polymers, and alloys used in additive manufacturing. As the 3D printing industry grows, the demand for smarter mixers capable of handling specialty feedstocks—like high-viscosity polymer slurries—also rises.
Accelerated Prototyping and Cost Savings
3D printing eliminates long lead times associated with machining or ordering custom parts. Engineers can iterate impeller designs—varying blade angles, curvature, or surface roughness—and test them the next day. Combining DFAM methodologies (like topology optimization and part consolidation) with rapid prototyping reduces both risk and development costs.
Case Study: Turbulence Promoters in Static Mixers
Researchers have leveraged 3D printing to test different turbulence-promoting geometries within static mixer channels. One experiment using twisted-tape and Kenics configurations saw a 130–140% improvement in membrane flux, a result of optimal mixing and reduced fouling arxiv.org. This approach allowed teams to evaluate multiple designs affordably—highlighting 3D printing's agility in testing real-world conditions.
Design for Additive Manufacturing (DfAM) in Mixing
DfAM isn’t simply about printing—it involves intentional redesign of components to leverage printing's strengths. For mixing, DfAM could mean incorporating internal hollows for weight reduction, seamless mounting features, or multi-material zones (stiffer cores with wear-resistant surfaces). Such complexity is nearly impossible with traditional machining but easily achieved with modern printers.
Challenges and Considerations
While promising, 3D-printed mixing parts must meet requirements for chemical resistance, thermal stability, and surface finish. Post-processing—like coating or smoothing—can improve durability and hygiene compliance. Where strength is vital, metal additive manufacturing or hybrid designs (printed cores with machined edges) may be necessary to ensure performance under industrial loads.
The Future: Active Mixing in Additive Manufacturing
Looking ahead, researchers are developing 3D printers that mix materials in situ—blending different filaments or powders during printing to create gradient materials or coatings. These innovations blur the lines between mixing and printing, potentially creating devices that combine manufacturing and mixing in a single step.
Conclusion
3D printing is not a passing trend—it’s a transformative force in the design of mixing equipment components. From prototyping new impeller geometries to manufacturing complex static mixers and turbulence promoters, additive manufacturing accelerates innovation and delivers performance gains. Designers can now iterate faster, scale more efficiently, and create custom solutions once considered impossible. If you’re interested in leveraging 3D printing for your mixing equipment needs, reach out for guidance and support.

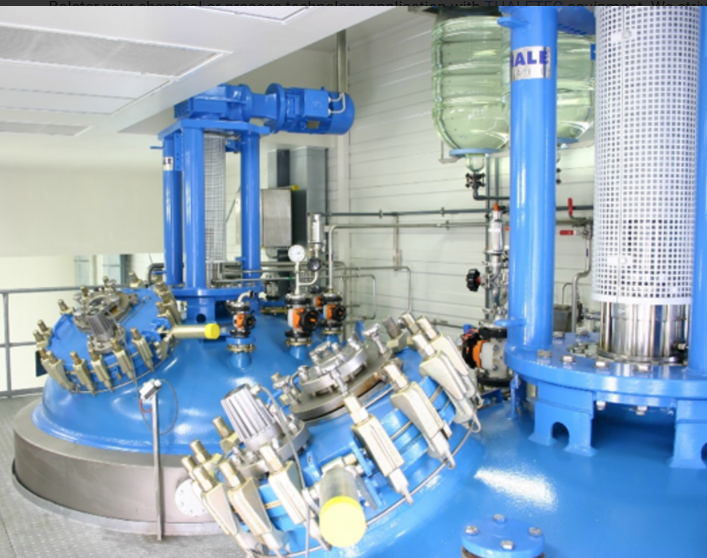