What Are Glass‑Lined Reactors and Why Are They Used in Chemical Processing?
Glass-lined reactors have become indispensable in chemical processing thanks to their superior corrosion resistance, purity, and versatility. In this comprehensive guide, we'll explore what makes these reactors unique, the core benefits they offer, typical applications, and key considerations when choosing the right glass-lined vessel for your process.
What Is a Glass-Lined Reactor?
Glass-lined reactors are industrial vessels constructed with a steel shell and an internal borosilicate glass coating. This fusion combines the mechanical strength of steel with the chemical resistance and inertness of glass. Available in single-, double-, or three-layer designs, the glass lining is thermally fused onto a prepared steel surface, ensuring optimal bonding and durability. These reactors often include jacketed zones for precise temperature control, agitation systems, and ports for sampling, heating, or feed introduction—perfectly tailored to demanding chemical processes.
Corrosion Resistance and Chemical Purity
One of the primary reasons glass-lined reactors are preferred is their extraordinary corrosion resistance. The glass interior is impervious to acids, alkalis, and most organic solvents—outperforming stainless steel in hostile environments. This inert lining prevents contamination of the reaction material, ensuring product purity—especially crucial in pharmaceuticals and fine chemicals. For example, reactions involving strong acids such as nitric or sulfuric acid are safely contained within glass-lined vessels without compromising equipment integrity.
Thermal & Pressure Capabilities
Glass-lined reactors exhibit excellent thermal shock resistance, withstanding rapid temperature shifts thanks to the thermal properties of both glass and steel. Many models operate effectively under high pressures and temperatures—up to several bar and several hundred degrees—while maintaining structural integrity. Hybrid designs like De Dietrich’s VERI reactor optimize both heat transfer and reactor strength by pairing a glass head with a reinforced steel body.
Visibility & Process Monitoring
The transparency of glass-lined reactor tops allows operators to visually monitor processes without opening the system. Observation visibility aids in identifying issues early—such as foaming, phase separation, or mixing irregularities—and supports cleaning-in-place (CIP) validation. This visual advantage enhances process safety and helps avoid batch failure.
Versatility Across Applications
Glass-lined reactors support a wide spectrum of chemical processes:
- Chemical synthesis of acids, esters, and catalysts.
- Polymerization, resin formation, and material synthesis.
- Crystallization and distillation, with thermal control support.
- Pharmaceutical API and drug product manufacturing, due to high purity demands.
- Batch transfers between different chemistries, thanks to the glass’ chemical compatibility
Cost Efficiency & Longevity
Although initial costs may be higher than stainless steel reactors, glass-lined vessels tend to have significantly longer lifespans due to their corrosion protection. Their ability to handle a wide range of chemistries eliminates the need for multiple, specialized reactors—offering cost and space efficiency. With proper cleaning and maintenance, these reactors remain reliable for decades, reducing downstream expenses.
Sanitation and Cleaning Advantages
The glass lining’s smooth, non-stick surface resists residue buildup, simplifying both CIP and manual cleaning operations. Its inert nature reduces the risk of cross-contamination between batches—and it maintains product visibility during wash cycles. These attributes support compliance with cGMP and food-grade hygiene standards.
Design Considerations and Options
When selecting a glass-lined reactor, consider:
- Lining thickness—thicker glass offers greater durability but requires careful handling.
- Layer count—single, double, or triple lining offers varying levels of insulation, chemical compatibility, and thermal control.
- Reactor head styles—glass or steel, each affecting visibility and pressure capacity.
- Jacket options—CO₂, steam, or thermal fluid jackets support precise thermal management.
Case Study: Improving API Synthesis
A specialty chemicals company experienced corrosion in stainless steel reactors when producing an acidic API intermediate. Switching to a glass-lined reactor allowed continuous operation with minimal maintenance. Visibility improved reaction tracking, and the glass-lined surface reduced contamination risk, enabling faster batch transitions. Ultimately, product yield increased, equipment costs reduced, and downtime decreased—highlighting the practical benefits of glass‑lined technology.
When Stainless Steel May Still Be Preferred
Steel reactors may be acceptable when:
- Processing low-corrosivity materials at high pressures/temperatures.
- Budget constraints outweigh corrosion risks.
- Mechanical strength is prioritized over corrosion resistance.
However, for aggressive chemistries or purity-critical products, glass-lined reactors remain the superior choice.
Conclusion
Glass-lined reactors stand out in chemical processing for their combination of corrosion resistance, thermal control, visual monitoring, versatility, and cleanability. Industries from pharmaceuticals to petrochemicals trust glass-lined vessels to deliver high-performance, safe, and cost-effective production. If your process involves aggressive chemicals or requires uncompromised quality, glass-lined reactors offer the reliability and efficiency you need.
For help selecting or implementing a glass-lined reactor tailored to your operations—or to discuss compatibility with your process—reach out today to get started!.
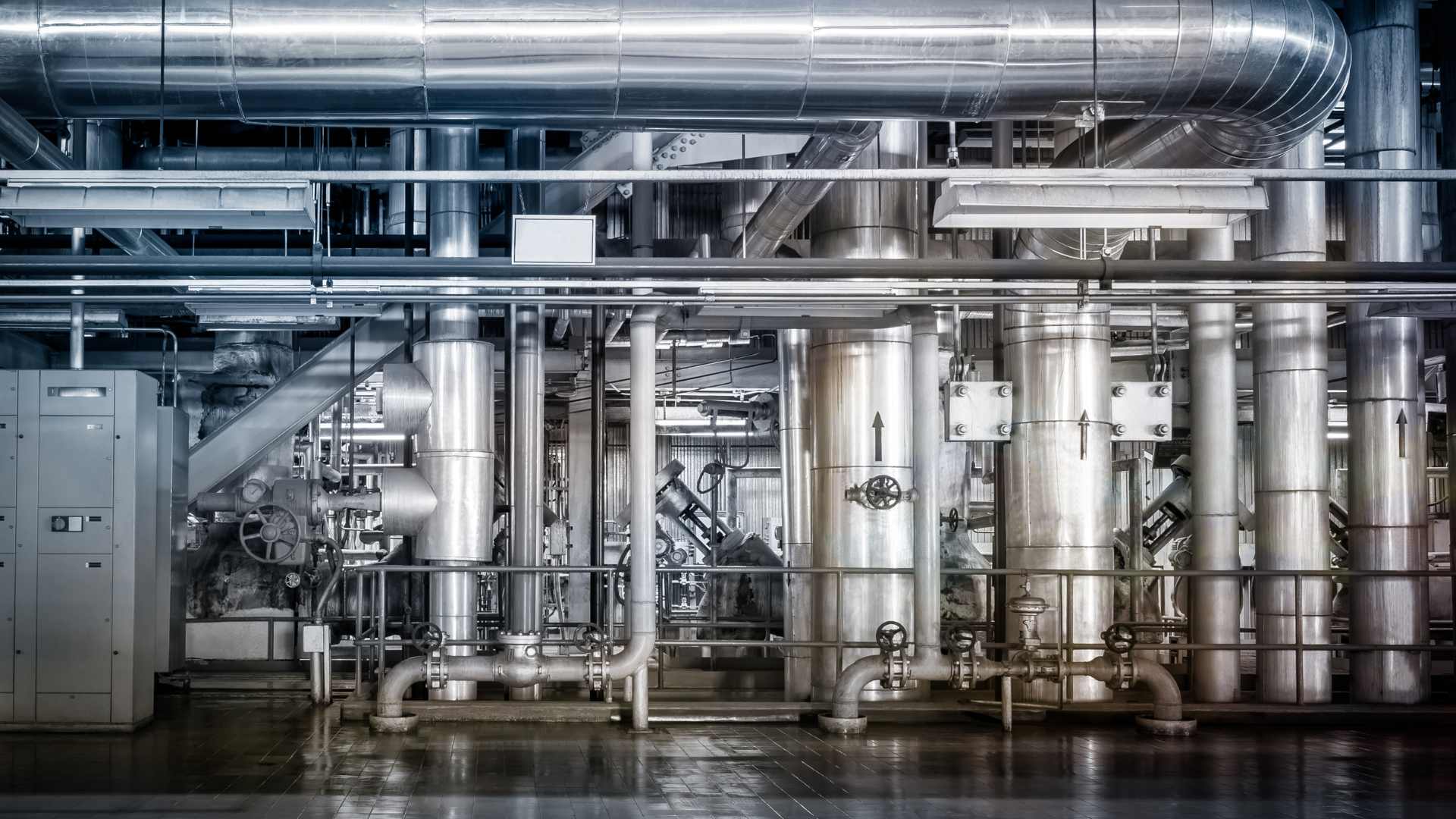
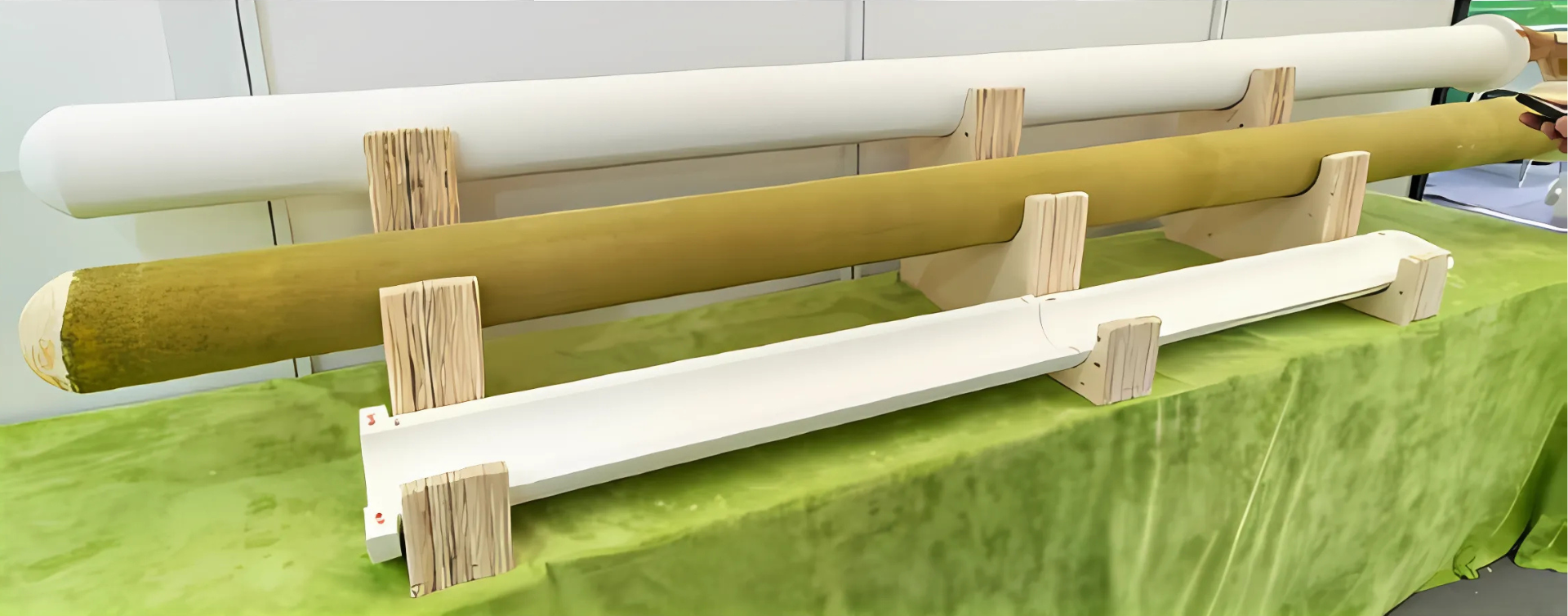
