Key Benefits of Using Glass-Lined Reactors in Pharmaceutical Manufacturing
Glass-lined reactors play a crucial role in pharmaceutical production due to their corrosion resistance, purity maintenance, and ease of cleaning. This guide explores the core benefits of glass-lined reactors in pharma, their design considerations, real-world applications, and how they contribute to regulatory compliance and operational efficiency.
What Are the Advantages of Glass-Lined Reactors in Pharmaceutical Manufacturing?
Glass-lined reactors are steel vessels coated internally with a thick layer of borosilicate glass. This unique construction combines the structural strength of metal with the chemical inertness and smooth finish of glass, offering key benefits for pharmaceutical manufacturing—enhanced durability, resistance to contamination, and easy maintenance.
Superior Corrosion Resistance
One of the primary advantages of glass-lined reactors is their exceptional resistance to corrosive substances. The glass lining protects the steel substrate from aggressive acids, alkalis, solvents, and cleaning agents, allowing reactors to remain operational longer than stainless steel equivalents. This corrosion resistance ensures consistent performance, avoids premature vessel failure, and helps reduce replacement costs.
Chemical Inertness & Product Purity
Maintaining high product purity is crucial in pharmaceutical production. Glass lining forms a non-porous, inert barrier that prevents metal ions from leaching into the product—a common issue with stainless steel reactors, which may result in undesirable catalytic effects. This chemical inertness aids in producing stable, uncontaminated batches, reducing risks of regulatory non-conformance.
Resistance to Thermal Shock
Pharmaceutical processes often involve rapid heating and cooling cycles. Glass-lined vessels resist thermal shock better than many metal alloys—thanks to the balance between steel’s strength and glass’s moderate expansion properties. This durability reduces cracking and stress, extending the service life of the equipment.
Operating Temperature & Pressure Range
Glass-lined reactors can operate across a wide range of temperatures and pressures—typically from sub-zero to over 300 °C and pressures up to full floor-level ratings. This versatility makes them suitable for varied unit operations like crystallization, distillation, and reflux in pharmaceutical production
Enhanced Transparency & Inspection Ability
Certain glass-lined systems feature glass reactor heads or sight glasses—allowing direct visual monitoring of processes such as mixing dynamics, bubbling, or foam formation without opening the vessel. This visibility enhances process control, safety, and troubleshooting while supporting regulatory traceability.
Regulatory Compliance & Cleanroom Integration
Glass-lined reactors meet cGMP and FDA standards through material traceability, smooth internals, and cleaning validation. The non-porous glass keeps surfaces free of potential contamination sites, easing compliance checks and simplifying sterile production procedures. Their easy cleanability further supports certified cleanroom operations.
Case Study: Optimizing API Batch Production
A mid-sized pharmaceutical manufacturer faced contamination and liner degradation in stainless steel reactors during API synthesis involving strong acids. Transitioning to a custom glass-lined reactor delivered immediate benefits:
- No liner corrosion within months
- Cleanability improved, reducing CIP cycle time by 30%
- Heavy metal contamination reduced to undetectable levels
- Process batch yield improved and variability minimized
This real-world example demonstrates how glass-lined reactors can safeguard product quality and reduce downtime.
Lifecycle and Cost Efficiency
Although initial costs are higher, glass-lined reactors offer superior lifecycle efficiency. Their corrosion resistance and durability often lead to less downtime, fewer repairs, and reduced demand for frequent replacements. Over time, these savings often justify the investment and deliver a better return on capital.
Challenges & Best Practices
Despite their advantages, glass-lined reactors require careful handling:
- Avoid impacts that could damage the glass lining.
- Maintain thermal profiles to prevent shattering or cracking.
- Perform regular inspection protocols (e.g., spark testing, visual inspection) to identify wear.
By adhering to best practices, reactors can provide reliable performance over decades.
Future Developments & Advanced Lining Technologies
Advances in glass chemistry and lining technology are focusing on:
- Enhanced alkali resistance to meet new cleaning standards
- Anti-microbial glass coatings to improve sterility
- Hybrid options combining glass-lined steel and transparent glass heads for visibility and strength.
Continued innovation ensures glass-lined reactors meet the next generation of pharma challenges.
Related Resources
- What is Glass-Lined Mixing Equipment? A Beginner’s Guide
- Static vs. Dynamic Mixing Equipment
- Maintenance Tips to Extend the Lifespan of your Mixing Equipment
Browse our guides to learn more about process improvements in pharmaceutical production.
Conclusion
Glass-lined reactors offer unmatched value in pharmaceutical manufacturing through their corrosion resistance, chemical purity, cleaning ease, and regulatory compliance. For API production, aseptic processing, or chemical synthesis, they are often the best choice. If you'd like guidance on selecting, sourcing, or optimizing glass-lined reactors, reach out to our experts and let us help you ensure success in your production processes.
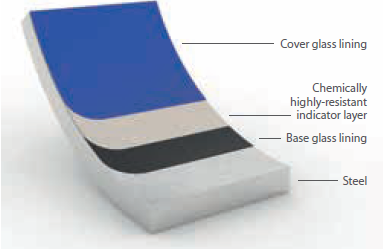
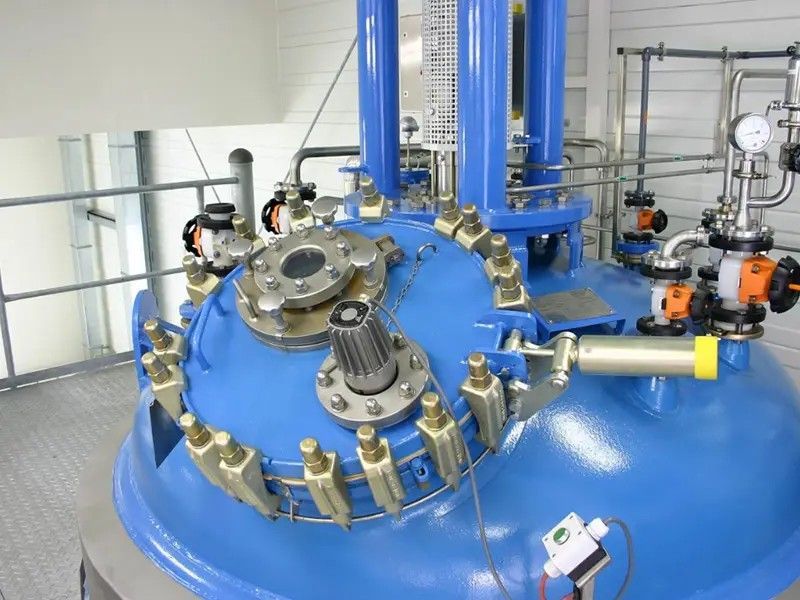
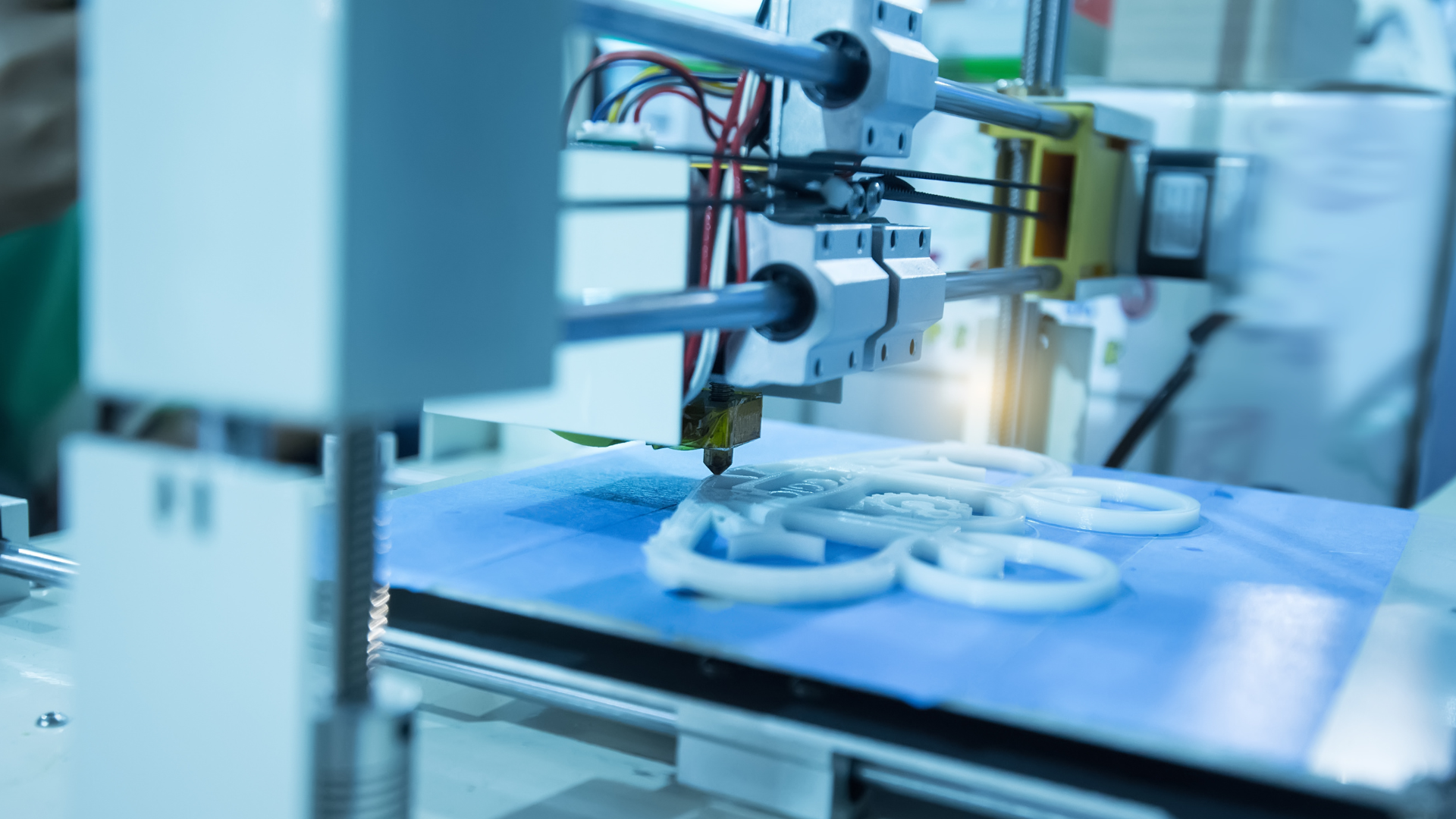